Author: Joey Clarke
Sand removal is undoubtedly a large contributor to upstream oil and gas operational costs. Wells produce significant amounts of sand during the drilling and fracking process as well as during initial production and throughout the well’s lifecycle.
When we think of sand, we usually only think of the erosion impacts that are associated with particulate in process, and that is warranted. On an operational level, sand poses a much higher operational cost simply from the capturing and maintenance of removing sand. Typically, customers rent or purchase expensive de-sanding equipment such as: sand screens, cyclones, or other technologies like settling tanks. These technologies require maintenance and disposals of the captured sand resulting in high operational costs without yielding 100 per cent effectiveness in removing the sand from fluid. Production impact is also a factor. During the maintenance of this equipment, wells are shut in, reducing production time. Settled sand in gathering lines and other production vessels reduces the capacity for production and adds higher maintenance costs and higher line pigging requirements for these assets.
The end user is now utilizing the acoustic monitors further to identify and qualify different de-sanding equipment, optimize wells for reduced sand levels, and help them identify and prioritize high sand producing wells for optimization.
Spartan Controls works with upstream oil and gas customers to reduce sand production and associated operational costs through well optimization. By utilizing Emerson Roxar Sand Acoustic Monitors, and powering the solution with SpartanPRO™ Connect, users can optimize well production to reduce sand production. The acoustic monitor enables us to monitor acoustic noise induced by sand falling out of process fluid (liquid, gas or multiphase) and impacting the pipe wall. This non-intrusive technology allows for real time tracking of sand production. Powering the solution with SpartanPRO™ Connect allows customers to have high acquisition rates with online interface for collaboration between integrity personnel and field operations.
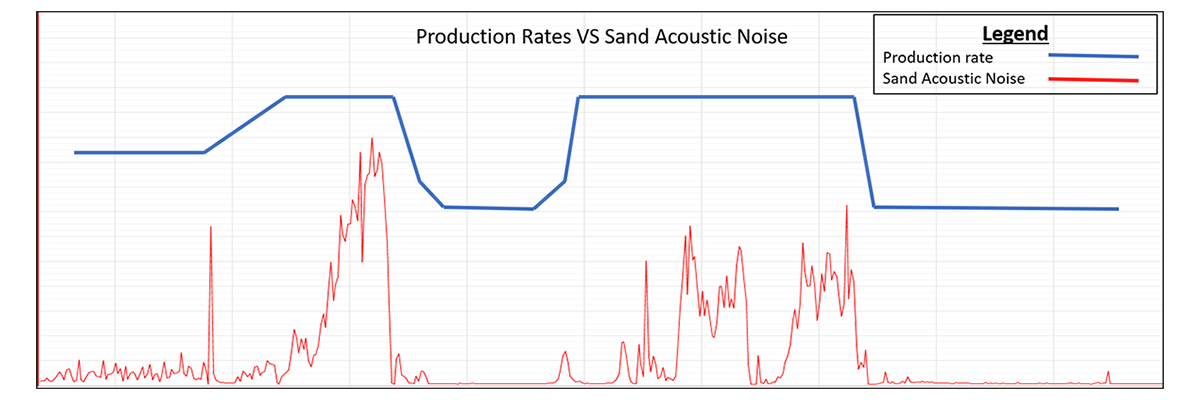
The customer used this theory and compared results with the acoustic system, which confirmed the same information they theorized. The end-user now utilizes acoustic monitors further to identify and qualify different de-sanding equipment, optimizes wells for reduced sand levels, and can identify and prioritize high sand producing wells for optimization, with the knowledge of exactly when de-sanding equipment is no longer necessary. These actions help the producer to reduce operational spend long-term while increasing profitability.
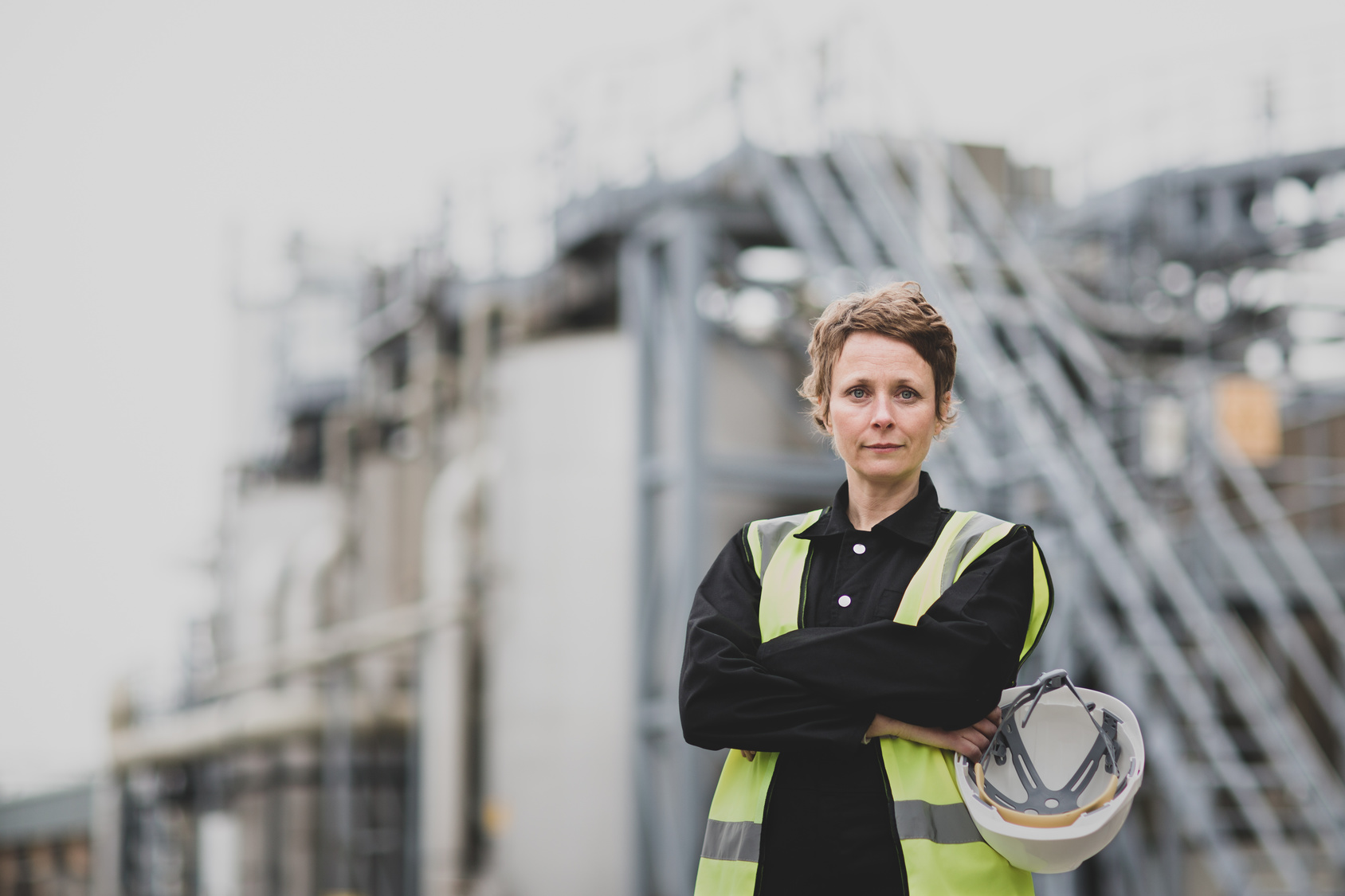