Author: Clary Keizer
Liquid Pipeline Surge is caused when rapid changes in flow rate occur. These pressure surges can be generated by anything that causes the liquid velocity in the line to change quickly. Such as the opening or closing of an automatic or manual valve, the starting or stopping of a pump or the emergency shutdown of an ESD device. It is because of these possible surge events that it is imperative to have a reliable surge relief system in place to prevent leaks, damages and even injury.
In this post we will discuss challenges and best practices when implementing a surge relief system as well as our very own Spartan solution and how we’ve overcome these concerns with an effective, user friendly design.
Liquid Pipeline Surge
As previously stated, surge events are caused when there is a rapid change is pressure due to a sudden change in flowrate. Some reasons for this are:
- Starting and stopping of pumps
- Valve closures
- ESD devices
These events can cause a wave of pressure that travels upstream and downstream of the event epicenter. This can create a 50psi rise per each foot of travel which can quickly exceed the maximum operation pressure (MOP) of the pipeline.
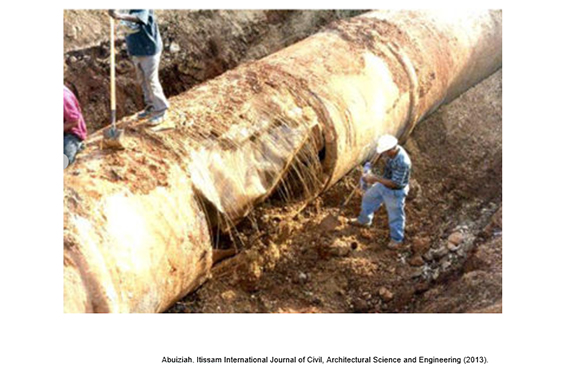
Effects of a surge event can be very dangerous. They can put lives at risk, have an impact on the environment and be very costly to repair. Some effects of surge events are:
- Piping Splits
- Flange Separation
- Weld Fatigue
- Pump misalignments
- Instrument failures
As you can see in this diagram, the difference in pressure in a liquid pipeline during a surge event with a relief system vs one without is significant. Plus, the speed at which the surge can happen takes just seconds. This means a fast-acting system which keeps the line protected should be a minimum requirement.
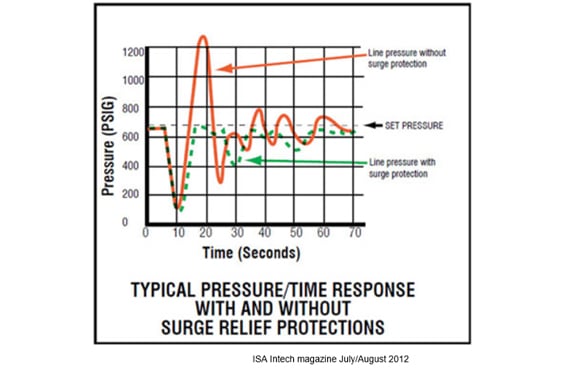
One of the most common methods of protection is utilizing a nitrogen loaded surge relief valve. Basically, the surge valve is set to match the operating pressure of the liquid pipeline, once the pressure within the pipeline exceeds that of the set pressure of the relief valve (surge event), the valve will quickly open allowing the liquid to pass through and typically end up in a holding tank. When the pressure from the event drops, the valve will then close slowly (so not to create another surge event) and operation will resume as normal.
The key to a high functioning relief valve is a nitrogen loading control system, otherwise known as a surge relief system.
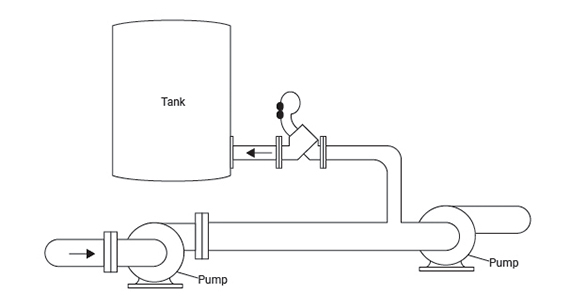
SpartanPRO™ Surge Relief System
What we found through compiled feedback from our customers are some key elements, requirements and nice to haves, and used this info as our design requirements within our own system. Some key features and benefits of our surge relief system are as follows:
- Very high accuracy of nitrogen pressure control
- Reliable surge overpressure protection, even at pipeline pressures close to maximum allowable operating pressures
- No setpoint drift normally associated with regulator-based designs
- Advanced dual PID pressure control
- Fully digital setpoints, alarm limits, deadbands
- Extremely low nitrogen consumption
- Up to 1 year per nitrogen supply cylinder
- The number of days of nitrogen remaining is continuously monitored
- Alerts and alarms on abnormal nitrogen supply and plenum pressures or excessive consumption
- Robust, fault tolerant design
- Redundant high-cycle solenoid valves
- Solenoid valve cycling duty optimization
- Abnormal event alarms
- Automatic preservation of plenum pressure on loss of power, loss of nitrogen supply, system fault detection
- Full colour touchscreen operator interface
- Intuitive graphic-based operation
- Fully configuration capability from screen – no laptop required
- Real-time and historical trends
- Low ambient temperature and bright sunlight display
- Advanced remote connectivity
- Local PLC connectivity (Modbus over ethernet)
- Cellular connectivity, including smart cell phones
- Monitor operation, events, trends, nitrogen consumption
- Receive alarms and alerts
- Remotely troubleshoot issues
- Download historical data, alarm summary
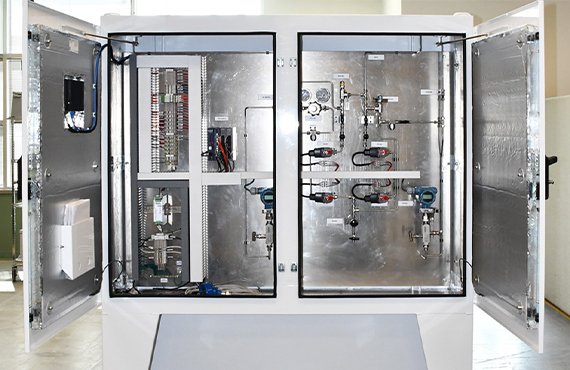
- Maximize product throughput to by enabling operation closer to pipeline pressure limits
- Eliminate setpoint drift associated with regulator-based systems
- Reduce operating costs by lowering nitrogen consumption
- Lower maintenance costs by reducing site visits
- Minimize unnecessary relief events by using reliable fault-tolerant system components
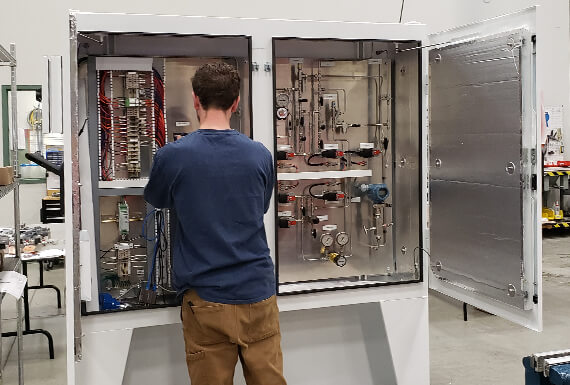
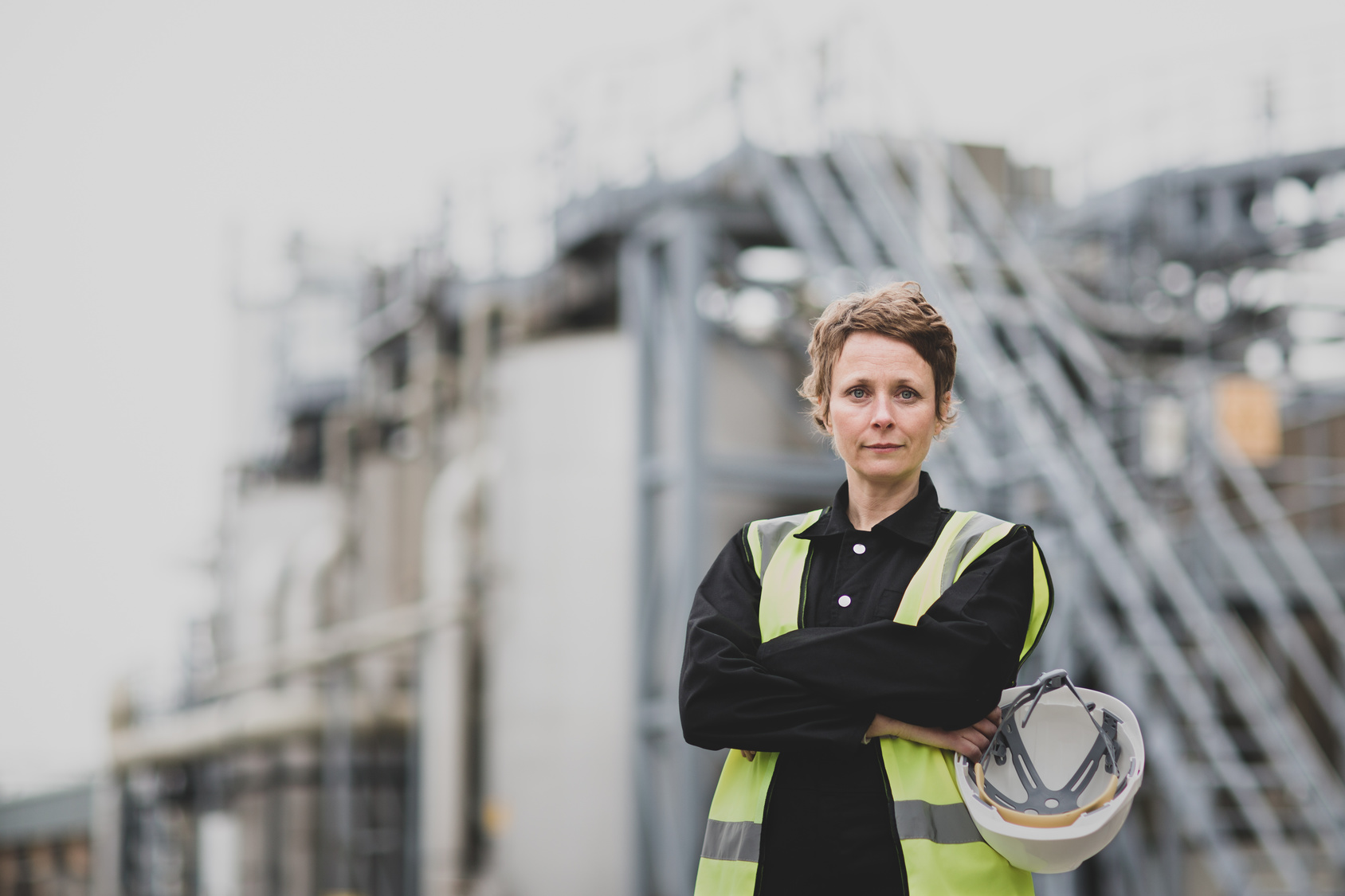